Choosing a GPS tracker for ready mix? Ask these 5 questions
Most GPS companies don’t know or care about the unique demands of transporting ready mix concrete, and that has real consequences for a concrete producer’s bottom line.
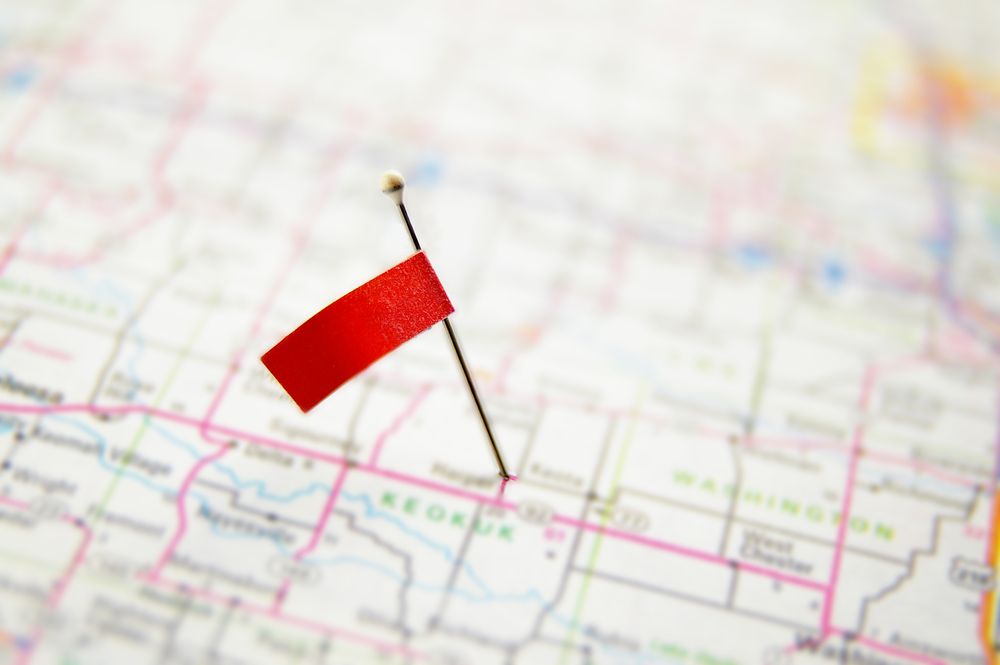
GPS tracking services are a dime a dozen. If you’ve ever considered outfitting your ready mix truck fleet with GPS, you know that even a casual search turns up an overwhelming number of options. The reality is that lots of industries need to track their employees or products from point A to B—but when it comes to ready mix trucking, that’s nowhere near the whole picture.
It’s easy to make the mistake of assuming that GPS companies are one-size-fits-all, but delivering a pizza or tracking a fleet of taxis is nothing like dispatching tens of thousands of pounds of perishable product to locations that don’t even exist on maps. Most GPS companies don’t actually know—or care—about the unique demands of transporting ready mix concrete, and that lack of understanding has real consequences for a concrete producer’s bottom line.
To avoid wasted minutes on the road, compromised concrete, and on-site bottlenecks, it’s vital to know what makes ready mix different and be prepared to ask for special features that go above and beyond the average GPS setup. Be sure to ask these five all-important questions to determine whether a GPS tracking service is right for your ready mix truck fleet:
1. Can I manually set geofencing without a street address?
Most GPS systems rely on data based on roads and street addresses—but what if the destination doesn’t actually “exist” on a map? If you’re pouring a subdivision that doesn’t have a house number, let alone a street name, then placing a geofence around the job site based solely on an address becomes a problem. Your GPS tracking service should allow you to easily set geofencing manually.
2. Can I tailor the shape of the geofence to the site?
Many job sites sprawl over large areas or are irregularly shaped; delivering ready mix to, say, the north end of a site versus the south could significantly alter a truck’s ETA. It’s essential to be able to customize geofences as much as possible to reflect what’s actually on the ground, so you can later report on how long the truck really took to arrive. Greater accuracy in your time logs means better scheduling of future trucks to that job site—and if you can shave off a minute here and there, per truck, per day, per month, per year, those savings will add up fast.
3. Is there a mechanism to count drum rotations?
Drum rotations, or “turns”, are an issue specific to ready mix trucks, which carry a product that requires mixing while in transit. It’s estimated that a full load of dry-batched ready mix concrete should undergo at least 200 turns before it can truly be considered “mixed”. Ready mix–focused GPS companies know this, and can fit your trucks with a mechanism to count the turns. Tracking turns allows you to be confident that the batch was sufficiently mixed before being discharged—if you start pouring blind, your concrete quality could suffer.
4. How can I tell when the truck starts pouring?
That same mechanism that tracks drum rotation can also tell you when the drum is rotating the other way and discharging concrete. While you may know when your truck arrived on site, the real question to keep your on eye on is “how long after arriving did they start pouring?” If it’s ten minutes or more, your customer may be asking for more concrete per hour than they can handle, and tying up your trucks in the process. They won’t care if you’ve got a couple trucks backed up on site, but you certainly do. If a customer is holding your trucks, that means they're coming back later, which pushes your schedule later, which makes you late for future loads and jobs.
5. Does the GPS system have an API?
An application programming interface (API) is basically a way for different pieces of software to talk to each other. No API means no syncing that GPS to your dispatch system of choice—and that means losing out on a ton of valuable data points. The more you know about your fleet’s movements, the better, so that any issues at a job site don’t become a chronic drain on your time and resources in the future. For instance, MPAQ’s Insight dispatch system uses an API to interact with GPS systems and record in real-time the precise moment a truck enters the geofence, starts pouring, finishes pouring, exits the geofence, and more. That data is then used to streamline future dispatches.
GPS tracking companies may like to tout themselves as all-purpose and versatile, but buyer beware: GPS features geared specifically to ready mix trucking will make a huge difference to the efficiency and profitability of your business. Asking the right questions early in your search will pay dividends at every stage of your dispatch operations in the future.